Obiekt budowlany – jaki jest, każdy widzi. Ale są takie
części konstrukcyjne, których nie widać, a są bardzo ważne
dla trwałości każdego budynku. Należą do nich fundamenty
oraz posadowione na nich ściany fundamentowe.
Właściwie zaprojektowane wymiary
oraz rozwiązania konstrukcyjne
fundamentów w bezpieczny
sposób przenoszą stałe i zmienne
obciążenia budynku na grunt. Dobór
fundamentu zależy nie tylko od rodzaju
i ciężaru budowli, ale również od cech
gruntu, na którym obiekt ma być posadowiony.
Prawidłowe wykonanie fundamentów
gwarantuje właściwe zachowanie
wybudowanych na nich pozostałych
elementów konstrukcyjnych. Jest to
pierwszy, chyba najważniejszy krok do
zapewnienia długowieczności obiektu
budowlanego. Dlatego do budowy
fundamentów i ścian fundamentowych
używamy materiałów o odpowiedniej,
zgodnej z założeniami projektowymi jakości,
oraz zatrudniamy do ich wykonania
tylko fachowców. Materiały powinny
posiadać odpowiednią wytrzymałość na
ściskanie, niską nasiąkliwość, mrozoodporność, a także muszą wykazywać
znaczną odporność na korozję chemiczną
i biologiczną.
Należy unikać materiałów nasiąkliwych,
takich jak ceramika poryzowana czy
pustaki ceramiczne o dużych, wolnych
przestrzeniach, ponieważ zabezpieczenie
przed działaniem wilgoci jest zbyt drogie
i ekonomicznie nieuzasadnione.
Głębokość posadowienia fundamentu
zależy od wielu czynników, m.in. od
głębokości przemarzania, poziomu wód
gruntowych i jest zawsze ściśle określona
przez projektanta.
Ściany fundamentowe i ściany piwnic
muszą być izolowane, zgodnie z założeniami
projektowymi. Najczęściej jest to
izolacja przeciwwodna wykonana według
zaleceń producenta.
RODZAJE FUNDAMENTÓW
Najczęściej wykonuje się:
+ fundamenty betonowe – gdy
budowle o małym obciążeniu,
+ fundamenty żelbetowe
najbardziej rozpowszechnione. Stosowane
przy średnim i dużym obciążeniu
oraz przy naprężeniach
dopuszczalnych na grunt poniżej
0,15 MPa. Zastosowanie w betonie
zbrojenia konstrukcyjnego zmniejsza
wymiary fundamentu w stosunku do
fundamentu betonowego. Zbrojenie
wzmacnia także odporność fundamentu
na nierówne osiadanie gruntu.
Wymiary ław, stóp fundamentowych
oraz potrzebną ilość zbrojenia określa
projektant na podstawie odpowiednich
norm.
Wybór dostępnych na rynku materiałów daje inwestorom duży wachlarz możliwości wykonania fundamentu, a jednak… najprostsze jest najlepsze. Dlatego najbardziej rozpowszechnionym materiałem do wznoszenia ścian fundamentowych oraz piwnicznych pozostaje bloczek betonowy. Najczęściej produkowany o wymiarach 12*24*38 cm (waga ok. 24 kg – zużycie 22 szt./m²) oraz 14*24*38 cm (waga ok. 28 kg – zużycie 19 szt./m²).
ZALETY BLOCZKÓW BETONOWYCH
Walory bloczków betonowych są powszechnie
znane większości wykonawców,
ale warto je przypomnieć:
+ relatywnie niska cena w porównaniu
z innymi rozwiązaniami,
+ łatwość montażu –
potrzeba specjalistycznego sprzętu ani
narzędzi,
+ szybkość wznoszenia
i czasochłonnego szalowania,
+ kontynuowanie prac na budowie –
2–3 dniach można wykonywać kolejne
etapy budowy,
+ jakość wyrobu – liczące się firmy produkują
bloczki na tzw. wibroprasach.
Zapewnia to wysoką wydajność i powtarzalność
produkcji. Gęstość brutto
utrzymana jest na poziomie około
2100 kG/m³,
+ wysokie parametry – technologia
oparta na naturalnych składnikach
mineralnych oraz cemencie
(CEM I 32,5R lub CEM I 42,5R) zapewnia
wysoką wytrzymałość na
ściskanie, niską nasiąkliwość, mrozoodporność,
znaczną odporność na
korozję chemiczną i biologiczną oraz
odporność na ogień – Euroklasa A,
+ wymiary – produkcja bloczków wymiary
tzw. wibroprasach zapewnia osiąganie
powtarzalnych, regularnych tolerancji
wymiarowych. Odporność na uszkodzenia
mechaniczne krawędzi, naroży
wpływa na oszczędność zaprawy podczas
murowania i oszczędność czasu
pracy.
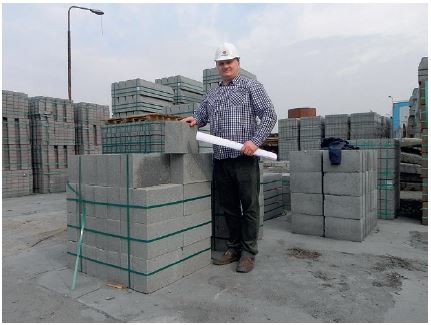
KERAMZYTOBETON
Oprócz najbardziej rozpowszechnionych
bloczków betonowych, część producentów
oferuje bloczki oraz pustaki
keramzytobetonowe. Keramzyt jest
kruszywem lekkim, który powstaje przy
wypaleniu gliny w temperaturze około
1200oC. Keramzyt charakteryzuje się odpornością
na wilgoć, niską temperaturę
oraz hamuje rozwój mikroorganizmów.
Przeznaczony jest do robót powyżej stanu
zerowego, jednak „przyzwyczajenie”
niektórych wykonawców skłania ich do
stosowania tego rodzaju bloczków przy
budowie ław fundamentowych, m.in.
ze względu na lekkość materiału. Bloczek
keramzytobetonowy 24*24*38 cm
waży ok. 28 kg, a jego zużycie wynosi
16 szt/m².
Na rynku spotykane są również bloczki
żużlobetonowe. Ich jedyną zaletą jest
cena. Ponieważ nie mają wysokiej wytrzymałości,
najczęściej stosowane są
do obiektów „mniej wymagających”, takich jak: altanki, komórki czy niewielkie
obiekty gospodarcze.
Alternatywą dla bloczków są również
pustaki szalunkowe, zasypowe. Pustaki
fundamentowe wytwarzane są z betonu
kruszywowego i pełnią rolę szalunku
traconego. Mają zastosowanie do ścian
fundamentowych konstrukcyjnych,
ścian piwnic oraz filarów i słupów. Pustak
szalunkowy betonowy o wymiarach
25*25*50 cm waży 22 kg/szt., a jego zużycie
wynosi 8 szt./m².
Pustak szalunkowy wykonany z keramzytobetonu
służy do stawiania ścian fundamentowych
o grubości do 36,5 cm.
Obecnie produkuje się pustaki szalunkowe
keramzytobetonowe na ściany proste
o wymiarach 365*500*250 mm oraz pustaki
szalunkowe narożne o wymiarach
365*610*250 mm.
Pustaki szalunkowe zasypowe najbardziej
rozpowszechnione są u naszych
południowych sąsiadów – Czechów. Wybierając
je pamiętajmy o prawidłowym
rozpoczęciu montażu tych pustaków –
pierwsza warstwa musi być dokładnie
wypoziomowana. Następnie układa się
kolejne, maksymalnie trzy warstwy pustaków,
a w wolne przestrzenie wlewa się
mieszankę betonową lub keramzytobetonową.
Wszystkie pustaki szalunkowe
można zbroić w pionie i w poziomie, jeżeli
takie są zalecenia projektanta. Wadą
są wysokie koszty wykonania – duża pracochłonność
w porównaniu z tradycyjnym
murowaniem z bloczków.
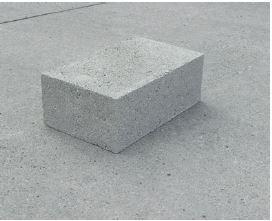
JAK MUROWAĆ BEZ BŁĘDÓW
Wszystkie warstwy bloczków układamy
na zaprawie cementowej. Pierwsza
warstwa zaprawy ma często różną grubość.
Wynika to z konieczności wypoziomowania
bloczków na niezbyt równych
ławach fundamentowych. Bloczki
zaczynamy murować od narożników,
a następnie dokładnie sprawdzamy ich
poziom niwelatorem lub poziomnicą
wężową. Nie należy w tym celu stosować
tradycyjnych poziomnic, gdyż ich
pomiar nie jest dokładny. Niewskazane
jest stosowanie różnych grubości spoin
między sąsiednimi bloczkami. Niedopuszczalne
jest pozostawienie spoin
niewypełnionych. Niedokładne ułożenie
zaprawy przyczynia się do obniżenia wytrzymałości
całej ściany, co może rodzić
problemy głównie na ścianach nośnych.
Osłabiona ściana może łatwiej pękać
na skutek dużych obciążeń użytkowych
i konstrukcyjnych. Niewypełnione spoiny
utrudniają również ich późniejszą
izolację pionową.
Aby zapewnić możliwie najlepszą wytrzymałość
całego układu ścian fundamentowych
nośnych, konieczne jest ich
przemurowanie na etapie wznoszenia
ścian. W tym celu, co drugi pustak ściany
wewnętrznej układa się bezpośrednio
w warstwie pustaków ściany zewnętrznej.
Takie murowanie ścian nośnych pozwoli
na ich trwałe połączenie i zachowanie
projektowanej sztywności układu
wszystkich ścian nośnych budynku.
Ważne jest, aby przed murowaniem kolejnej
warstwy bloczków dokładnie usunąć
zanieczyszczenia, np. pył powstający
przy docinaniu lub szlifowaniu innych
elementów na budowie. Zbyt duże zabrudzenie
na bloczkach uniemożliwi dobre
związanie zaprawy z kolejnymi warstwami
ściany. W konsekwencji może
nawet dojść do całkowitego „rozłączenia
się” sąsiednich warstw bloczków.
Normatywnie spoina pozioma nie powinna
być grubsza niż 12 mm, jednak
w praktyce grubość może wynosić od
10 mm do 15 mm. Niewskazane jest
stosowanie grubszych spoin, gdyż ich
wytrzymałość na ściskanie jest z reguły
znacznie mniejsza niż elementów ściennych
i przed ostatecznym stwardnieniem
może pękać.
Przy stosowaniu gotowej zaprawy, na
opakowaniu powinna być podana jej wytrzymałość,
aby można było porównać ją
z wytycznymi projektanta. Do gotowych
zapraw nie dodaje się kruszywa ani spoiwa,
gdyż mają one optymalne proporcje.
Przy murowaniu ścian fundamentowych,
które są szersze niż 38 cm stosuje
się przewiązanie poprzeczne. Jeśli ściany
fundamentowe murujemy w budynkach
podpiwniczonych należy je zawsze
usztywnić, dzięki czemu łatwiej przeniosą
napór gruntu. Wykonuje się to na dwa
sposoby: w półtorametrowych odstępach
ustawia się słupy żelbetowe lub podczas
murowania układa się w spoinach zbrojenie.
NA TO WARTO ZWRÓCIĆ UWAGĘ
Przy wyborze producenta warto zwrócić uwagę, czy używa on palet do transportu bloczków betonowych. Obecnie większość wytwórców nie stosuje palet – chyba, że jest to wyraźne życzenie inwestora. Wyroby bez palet są odpowiednio „paczkowane” i powiązane taśmami polipropylenowymi. Na budowie takie „paczki” są rozładowywane przy pomocy samochodu z HDS, wyposażonego w chwytaki. Ogranicza to koszty i ułatwia pracę – palety na budowie często ulegają zniszczeniu a zniszczone nie podlegają zwrotowi. Warto również zwrócić uwagę na takie aspekty, jak dystrybucja, profesjonalna obsługa budowy przez dostawców (hurtownie), sposób składowania materiałów budowlanych. Najlepsi producenci współpracują z solidnymi dystrybutorami, aby zapewnić fachową obsługę budowy, a w rezultacie zadowolenie inwestora.